The Boeing 737 MAX crisis highlights the consequences of corporate culture issues, supply chain mismanagement, and design errors. To regain public confidence, Boeing needs to make drastic changes now before costing more lives.
Public concerns about Boeing's safety have increased after a fuselage panel of its 737 Max 9 detached during an Alaskan Airlines flight on January 5. Then there are new concerns about the potential risks with the anti-ice system on the new 737 Max 7 that can overheat and cause the engine nacelle to break apart and fall off. To address this concern, Boeing withdrew its request for a safety standard exemption for the 737 MAX 7 on Jan. 29, likely delaying its delivery by two years.
The safety issues, including two fatal crashes involving the 737 Max 8 in 2018 and 2019, have been linked to broader problems dating back to the development of the 787 Dreamliner during the early aughts. These issues are rooted in Boeing's culture, supply chain management, and product design.
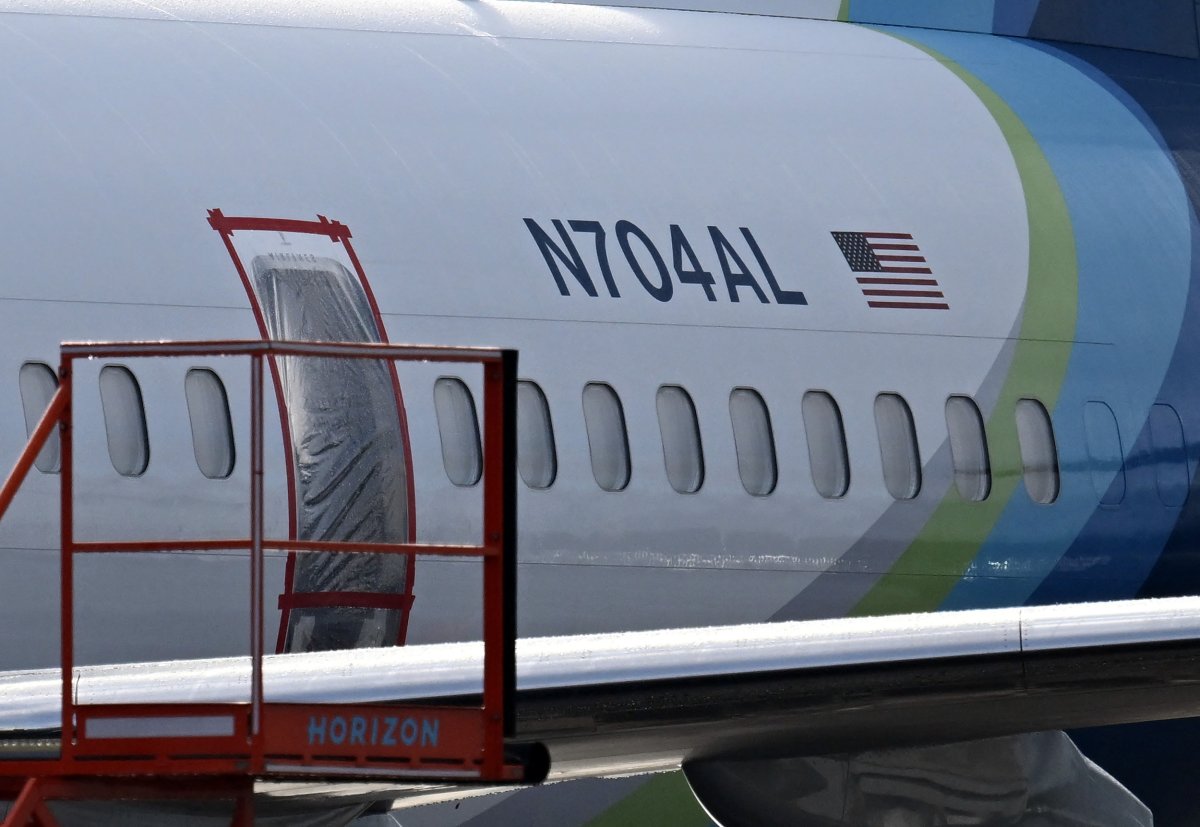
McDonnell Douglas influenced Boeing's culture
Established in Seattle in 1916, Boeing was initially an engineering-centric firm specializing in the design, manufacture, and sale of airplanes. However, a significant cultural shift occurred when Boeing merged with another airplane manufacturer, McDonnell Douglas (MD), in 1997 and relocated its headquarters to Chicago in 2001.
This merger led to conflicts between Boeing's dedicated engineers and MD's savvy finance and marketing executives. As the board of the merged company began to favor promising financial projections, Boeing underwent a transformation into a lean organization. A bold step was taken in 2005 when Spirit Aero in Wichita, Kansas, was divested by Boeing and sold to private equity investors to enhance financial performance.
Boeing's shift from an engineering focus to a finance focus led to a change in priorities. Business performance measures such as return on assets, cost reduction, and time-to-market began to take precedence over engineering designs, production process designs, and supplier management. This finance-oriented mindset significantly influenced the development approach for Boeing's 787 Dreamliner and 737 Max.
Boeing's extensive outsourcing strategy via modular design
In the development of the 787 Dreamliner, Boeing deviated from its traditional supply chain strategy, where suppliers produced parts designed by Boeing engineers for assembly. Instead, Boeing outsourced 70 percent of the design, engineering, and manufacturing of entire modules to more than 50 strategic partners. These partners were expected to deliver complete modules, such as fuselage panels and electrical systems, for final assembly at Boeing's factories.
While modular designs can be cost-effective with a well-designed product and experienced partners, these conditions were not met. There was a lack of communication and coordination among the partners, and many lacked the necessary expertise in design, engineering, and supply chain management.
The goal of this extensive outsourcing strategy was to keep the development budget at $5.5 billion and the development time at 5 years. However, without adequate investment in supply chain management capabilities, Boeing faced issues, including major delays and fire hazards from its lithium battery system. Ultimately, the 787 development program was three years late and cost more than $32 billion.
In addition to time and money, there are ongoing safety concern about the epoxy tape used to connect the wings and the middle-fuselage, and the inspection and maintenance of the 787's composite structure, which may require x-ray or ultrasound equipment
Boeing's saga continues
Similarly, the Boeing 737 Max, the fourth generation of the Boeing 737 family, was designed to compete with the Airbus A320neo, boasting improved fuel efficiency, lower operating costs, and an increased range. However, investigations following two fatal crashes involving its 787 Max 8 revealed that a malfunctioning software system, the Maneuvering Characteristics Augmentation System (MCAS), was a key contributing factor to the crashes. The MCAS, designed to prevent stalling by automatically pushing the nose down under certain flight conditions, relied on a single angle-of-attack (AOA) sensor. This could provide erroneous data, triggering unwanted nose-down movements. Furthermore, pilots were not adequately informed or trained about the MCAS and how to override it in case of failure. Boeing has since developed an MCAS software update to provide additional protection if the AOA sensors provide erroneous data.
The recent investigation into a door plug that detached from a brand new 737 Max 9 mid-flight is particularly concerning. On Jan. 30, Boeing and other industry officials suggested that the bolts required to secure the fuselage panel of an Alaskan Airlines plane appeared to be missing when the plane left Boeing's factory. This incident may have been caused by paperwork and process lapses at Boeing's Renton factory in Washington.
While this may seem like a rare incident, it exposes a flaw in Boeing's quality control process. The absence of bolts or components in a finished product indicates a failure in the fool-proof process known as Poka-Yoke in the Toyota Production System, designed to prevent mistakes
Looking ahead
To regain public trust, Boeing requires a comprehensive transformation. Organizational changes should include a shift towards a safety-first culture, enhanced ethical standards, robust whistleblower protections, strengthened audits and reviews, and improved stakeholder communication and collaboration. Operationally, improvements in supply chain management are necessary, including quality assurance and control, reduction of complexity and variability, better coordination and integration, and investment in research and development. From a product perspective, Boeing should enhance its design by integrating cutting-edge technology, adopting a user-centric approach, conducting thorough testing and verification, and providing comprehensive training and documentation.
As a symbol of American aviation leadership for more than a century, it is imperative for Boeing to enhance its performance and reputation while prioritizing the safety of its passengers and crew over financial returns.
Christopher Tang is a university distinguished professor at the UCLA Anderson School of Management.
The views expressed in this article are the writer's own.
Uncommon Knowledge
Newsweek is committed to challenging conventional wisdom and finding connections in the search for common ground.
Newsweek is committed to challenging conventional wisdom and finding connections in the search for common ground.